The increasing presence of robotics in the workplace has significantly reshaped the way businesses approach safety and employee well-being. While automation and robotics offer numerous advantages in reducing workplace injuries and hazards, they also introduce new risks that must be carefully managed.
In this comprehensive guide, we will explore both the positive and negative impacts of robotics on workplace safety and health, as well as strategies to mitigate risks and optimize employee safety.
How Robotics Enhances Workplace Safety and Health
Reducing the Risk of Falls from Heights
One of the major benefits of robotics is its ability to reduce the risk of workplace falls, particularly in warehouses and industrial facilities. Automated robotic systems can retrieve or store items located at high elevations without requiring human intervention. This minimizes the need for employees to operate aerial lifts or climb ladders, significantly decreasing fall-related injuries.
Minimizing Musculoskeletal Disorders (MSDs)
Repetitive motion injuries, such as musculoskeletal disorders (MSDs), are among the most common workplace ailments. Robotics, particularly exoskeleton robots and automated systems, can assist with physically demanding tasks. These machines help employees avoid excessive strain caused by repetitive movements, ultimately reducing injury rates and improving overall workplace health.
Eliminating Heavy Lifting Injuries
Heavy lifting is a leading cause of workplace injuries, particularly in manufacturing and logistics. Robotics can take over the lifting and transporting of heavy materials, minimizing the strain on workers. By reducing manual lifting, companies can lower the risk of back injuries and related health issues, leading to fewer workers’ compensation claims and improved employee well-being.
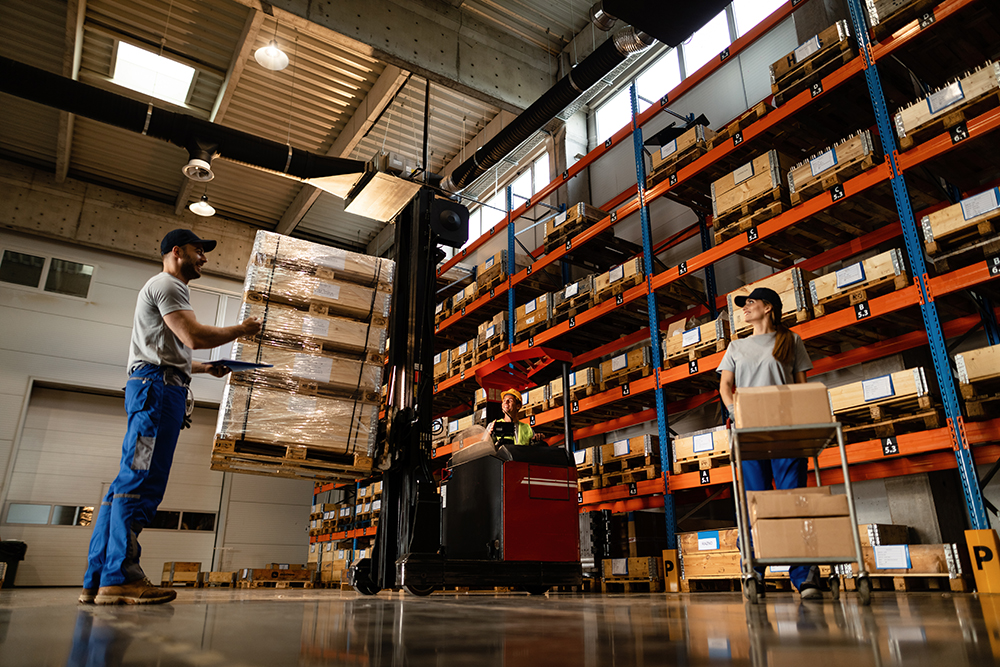
Low angle view of happy warehouse workers communicating while working with shipment in industrial storage compartment.
Preventing Fatigue-Related Injuries
Human fatigue is a significant factor in workplace accidents. Studies show that workers who are tired or overworked are at a greater risk of injury. Unlike humans, robots do not experience fatigue, allowing them to maintain consistent performance over long shifts. Automated systems can handle repetitive and strenuous tasks, reducing the likelihood of mistakes and injuries caused by worker exhaustion.
Ensuring a Safer Environment in Hazardous Industries
In industries such as chemical manufacturing, mining, and construction, workers are exposed to dangerous environments that can pose serious health risks. Robotics can perform tasks in these hazardous conditions, keeping employees out of harm’s way. Automated machinery can handle toxic substances, operate in extreme temperatures, and perform precision work in areas where human workers would face significant risks.
Hazards and Risks Associated with Workplace Robotics
Despite the benefits, robotics also introduces new workplace hazards. While these risks can be mitigated with proper precautions, it is crucial for employers to recognize and address them effectively.
Accidents from Human-Robot Interaction
While robots are designed to improve safety, improper interaction between humans and automated systems can lead to accidents. Workers may accidentally enter the operating zone of a moving robot, leading to potential injuries. To prevent this, safety protocols such as restricted zones, emergency stop mechanisms, and training programs must be implemented.
Failure to Follow Safety Procedures
Robotic systems often come with safety features such as sensors and emergency stops, but these are only effective when used correctly. Workers must be adequately trained on how to interact safely with robotic machinery. Lack of awareness or misunderstanding of emergency procedures can result in severe accidents, as seen in documented cases where failure to activate emergency stops led to fatal incidents.
Increased Ergonomic Risks
While robots reduce physical strain on workers, new ergonomic risks can arise from prolonged interaction with robotic systems. Employees who oversee robotic operations may develop strain injuries from extended use of control systems or monitoring screens. Ergonomic assessments should be conducted regularly to ensure that workstations are designed to support employee well-being.
Exposure to New Technological Hazards
Modern robotics often incorporate advanced technologies such as artificial intelligence, machine learning, and automation software. These technologies may expose workers to new risks, such as electromagnetic fields, laser emissions, or electrical hazards. Proper safety measures, such as protective equipment and shielding, should be implemented to mitigate these risks.
Lack of Understanding and Training
One of the biggest challenges of integrating robotics into the workplace is ensuring that employees are well-trained in robot operation, safety procedures, and troubleshooting. Inadequate training can lead to misuse, accidents, and operational failures. Employers must invest in ongoing training programs to ensure their workforce is equipped to handle robotic technologies effectively.
Best Practices for Workplace Robotics Safety
Implementing Comprehensive Safety Training
To ensure a safe work environment, employees must receive thorough training on how to operate and interact with robotic systems. Training should cover emergency shutdown procedures, hazard recognition, and safe handling practices.
Regular Safety Inspections and Maintenance
Routine maintenance of robotic systems is crucial to preventing malfunctions that could lead to workplace accidents. Employers should establish regular inspection schedules and ensure that all robotic equipment is functioning properly.
Developing Clear Safety Protocols
Organizations should establish clear guidelines and protocols for working alongside robotic machinery. This includes defining restricted areas, implementing warning systems, and ensuring that safety barriers are in place to prevent unauthorized access to robotic work zones.
Monitoring and Assessing Workplace Safety Continuously
Employers should continuously assess the effectiveness of workplace robotics safety measures. Regular risk assessments, employee feedback, and safety audits can help identify potential hazards and improve safety procedures over time.
Future of Robotics and Workplace Safety
As robotics technology continues to evolve, so will workplace safety practices. The National Institute for Occupational Safety and Health (NIOSH) has established the Center for Occupational Robotic Research, which aims to enhance knowledge on how to safely integrate robotics into various industries. Research and regulations will continue to develop as robotics become more advanced and widespread.
With the right approach, robotics can revolutionize workplace safety, significantly reducing injuries and improving efficiency. However, businesses must remain proactive in addressing new risks and ensuring that workers are well-equipped to operate alongside robotic technologies safely.
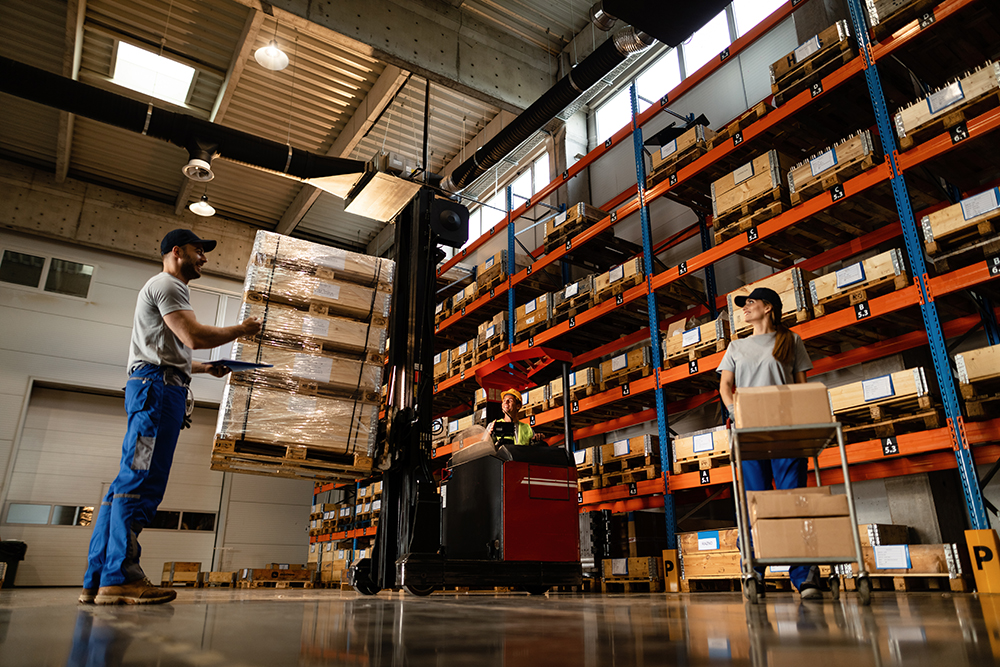
Low angle view of happy warehouse workers communicating while working with shipment in industrial storage compartment.
Robotics in the workplace presents both immense opportunities and new challenges. While automation can enhance safety and reduce physical strain, it also introduces new hazards that require careful management. Employers must take a balanced approach—leveraging the advantages of robotics while implementing rigorous safety measures.
By prioritizing employee training, enforcing strict safety protocols, and continuously evaluating risks, businesses can create a safer, more efficient, and technologically advanced workplace.